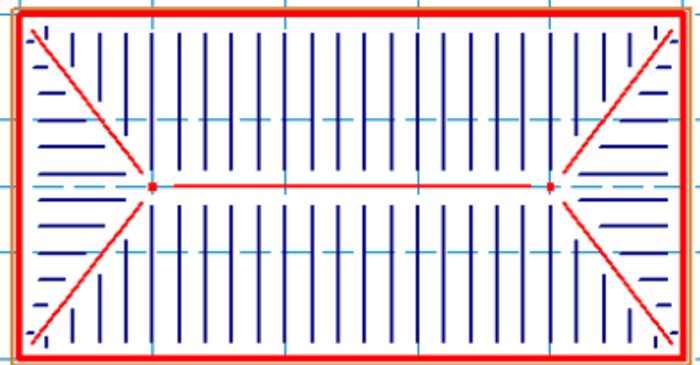
May 26, 2011
How to Represent Trusses in RISAFloor Model Without Modeling the…
Using this method in RISAFloor, we are not actually designing the trusses, but just adding “dummy” bottom and top chords to correctly calculate the loading and help distribute the loads to the walls.