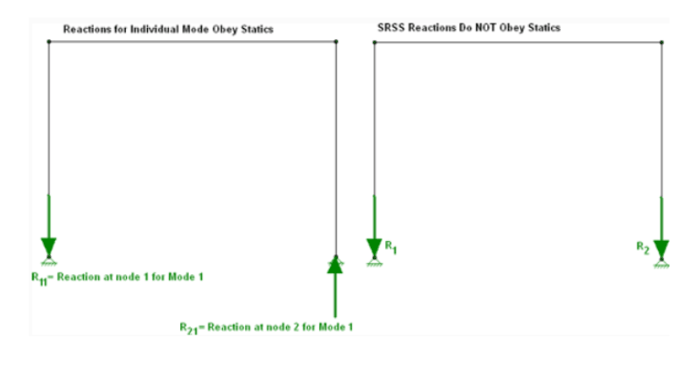
April 3, 2012
Why Don’t My Response Spectra Reactions Satisfy Statics?
The applied loads in a response spectrum analysis (RSA) are the applied masses times the accelerations in the response spectra. Each mode of vibration produces its own set of joint reactions. The reactions for each mode obey statics as shown in the portal frame example shown below: Response...