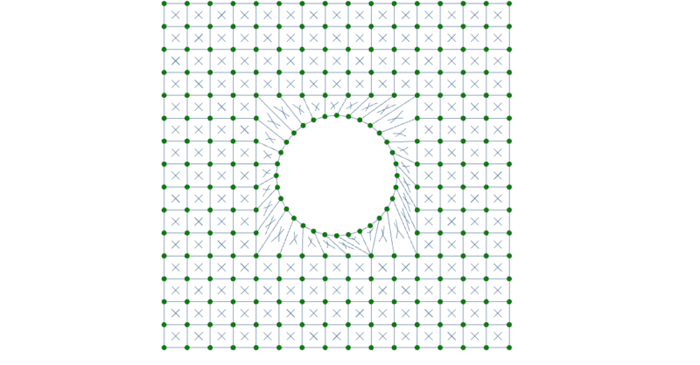
June 16, 2011
How to Model a Hole in a Plate
While RISA-3D (or RISA-2D) does not have an explicit tool to punch a hole in a plate, you can use the following steps to manually model them:
In structural engineering, few design challenges are as rewarding—or as unforgiving—as the tall building. While gravity systems and code checks form the backbone of any structural project, once a structure rises beyond ten or fifteen stories, a shift occurs. Wind and seismic forces begin to dominate. Story drift and torsional irregularities become non-negligible. Load paths grow increasingly indirect. And design decisions, if not carefully made early on, can have exponential consequences higher in the structure. Tall buildings are not simply “bigger” versions of short ones. They behave differently. And understanding those differences is essential for any engineer working in an urban environment where building vertically is often the only viable path forward. Modeling for Reality, Not Just Code The foundation of any successful tall building design lies in the model—its assumptions, resolution, and degree of abstraction. Many engineers begin with simplified representations: rigid diaphragms, idealized connections, and linear material properties. This is practical and often sufficient for early design phases. But as the building increases in height and complexity, those assumptions may start to mask critical behaviors. Semi-rigid diaphragm modeling, for instance, allows engineers to capture in-plane flexibility of floor systems—especially important in buildings with irregular cores, open floor plans,…
Read More
While RISA-3D (or RISA-2D) does not have an explicit tool to punch a hole in a plate, you can use the following steps to manually model them:
Have you ever received an instability warning when running a three dimensional RISA-3D model? This is because RISA-3D cannot build the stiffness matrix with the configuration you have modeled. In some cases, your model is truly unstable and in others it’s a matter of correctly modeling your...
In RISAFloor on the roof level, you layout only the top chords of the truss and create your slope. These top chords by themselves probably won’t be sufficient enough to get designed in RISAFloor, but, don’t worry, we’ll take care of that in RISA-3D when we model the rest of truss.
In RISAFloor, the beams are susceptible to two forms of buckling; Euler buckling and lateral-torsional buckling. The unbraced length is determined in RISAFloor using the deck properties and framing.
Using this method in RISAFloor, we are not actually designing the trusses, but just adding “dummy” bottom and top chords to correctly calculate the loading and help distribute the loads to the walls.
It’s easy to apply tapered surface loads to plates in RISA-3D by stepping up the loads from one level to the next.
In RISA-3D you can automatically apply notional loads to your structure to comply with your steel code (such as AISC 360). Notional loads take into account a building’s actual out-of-plumbness by adding de-stabilizing lateral loads. The AISC 360 recommends either 0.2% or 0.3% of the vertical loads...
When running a truss model in RISA-3D or RISA-2D, it’s quite common to receive an instability warning, but these can be easily resolved by following a few simple rules.
In Aluminum design, the welded areas have a decreased material strength and RISA-3D can assign any material strength to the members based on the Material spreadsheet.
Our monthly "Structural Moment" newsletter is the best way to keep up with RISA’s product updates, new releases, new features, training events, webinars and more...