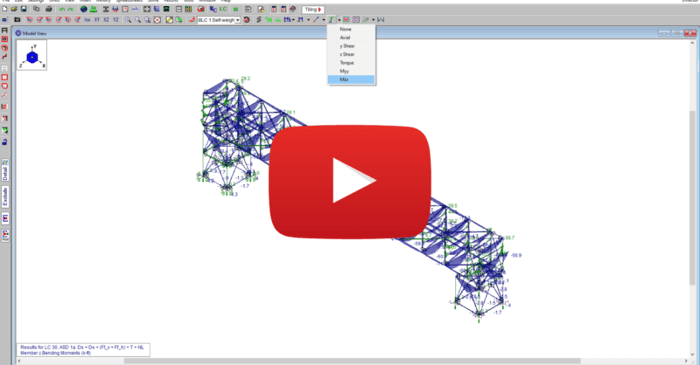
June 15, 2015
Improved Result Access in RISA
This video tutorial will demonstrate how to find quickly review the results in RISA-3D in order to optimize the design.
We often get asked: “Should I model my foundation as a slab or a spread footing in RISAFoundation?” While both are valid options, they use very different analysis methods, and the results can vary accordingly. In this article, we’ll walk through a side-by-side comparison, using the same modeled conditions to highlight how the results differ — and why. Model Setup To keep things consistent, we modeled a single condition in two ways: once with a spread footing and once with a mat slab. Mat Dimensions: 10' x 10' x 1' Pedestal: 1' x 1' x 2' Loads Applied: 40 k vertical dead load 10 k lateral dead load 15 k lateral wind load 14.79 k concrete self-weight Soil Overburden: Set to 0 for both elements Slab Mesh Size: Refined below default for more detailed results Load Combinations: A basic set used for clarity (see screenshots in RISAFoundation) Analysis Methodology Feature Spread Footing Slab Element Analysis Type Rigid body Finite Element Analysis (FEA) Support Model Single support point Compression-only springs (based on subgrade modulus) Mesh Behavior No submesh Submeshed into smaller plate elements Lever Arm for Lateral Loads Spread Footings: Full pedestal height + full footing thickness Slabs: Full pedestal height…
Read More
This video tutorial will demonstrate how to find quickly review the results in RISA-3D in order to optimize the design.
With the new release of RISA-3D v13.0, you now have the ability to include moving load combinations in a Batch solution. Just select which load combinations you want included in the Batch solution using the “Solve” checkboxes in the Load Combinations spreadsheet.
RISA-3D v13 includes a new Ritz Vector Solver for the Dynamic analysis. When running a Response Spectrum analysis for seismic design, some structures experience large numbers of local modes that don’t contribute to the lateral response of the structure. The use of load-dependent Ritz vectors...
Cold Formed Steel channels are often built-up as back-to-back sections to help strengthen them. RISA-3D can design the Cold Formed Steel back-to-back channel and track sections. The Shape Selection dialog will allow you to model the built –up sections by selecting “Back to Back” shown below.
Timber design per the Canadian CSA 086-2009 design code is now available. Canadian wood member design is very similar to the US NDS member design. There are slightly different load factors, material properties, shape tables, and capacity equations, but the overall modeling procedure in RISA is the...
New codes have been added to RISA-3D v13 and RISAFloor v9, these include: AISI S100-12: Cold-Formed Steel Design Code CSA 086-09: Canadian Wood Design Code ACI 530-13: Masonry Design Code To select these codes for your design, simply choose them from the Codes tab of Global Parameters:
RISA-3D and RISA-2D come with a default list of existing moving load patterns. These are listed in the Moving Loads Library which can be viewed by clicking on the Moving Load Patterns button in the Advanced tab.
The Load Combinations spreadsheet in RISA-3D is limited to ten columns of BLC and Factor combinations. However, there are times where you may need to include additional entries to your Load Combination. To do this, you can simply “nest” your load combinations.
After solution in RISA-3D, you can use Results View Settings to view the Plate Contours graphically on your model.
Our monthly "Structural Moment" newsletter is the best way to keep up with RISA’s product updates, new releases, new features, training events, webinars and more...