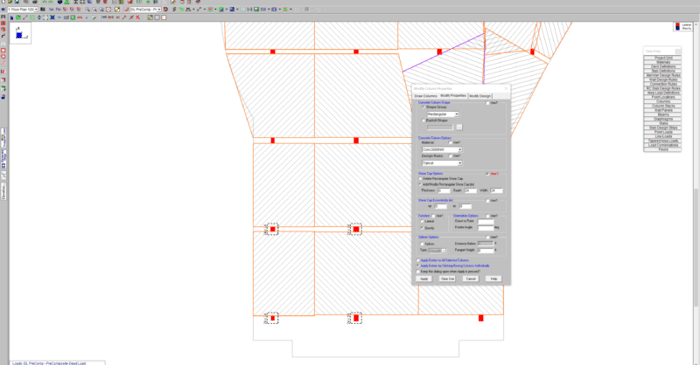
January 2, 2014
Adjusting Slab Thickness in RISAFloor ES
In structural steel projects, the transition from design to fabrication is a common source of coordination challenges. One of the biggest pain points? Connection design. Whether it’s miscommunication on end reactions or unclear design intent, connection assumptions can break down in the gap between engineering and detailing. By using RISA-3D and RISAConnection—and leveraging direct integrations with SDS2 and Tekla Structures—structural engineers can streamline the handoff to fabricators, reduce errors, and improve collaboration. This post walks through how to support real-world coordination using these tools in practice. 1. Model and Analyze the Steel Frame in RISA-3D Start by building your structural steel frame in RISA-3D. Define geometry, assign member sizes, apply loads, and analyze the model. Once you're satisfied with the analysis results, RISA-3D provides the connection forces—axial, shear, and moment reactions—for each member end. 2. Export Connection Forces to RISAConnection Next, send selected members and their design forces to RISAConnection. This direct integration eliminates the need to manually transfer loads or recreate geometry. Once in RISAConnection, you can: Choose from a library of shear, moment, and braced connections Model the full geometry, including bolt patterns, welds, and gusset plates View pass/fail results for each limit state, with clear failure mode…
Read More
Use RISASection to find the properties of built-up steel sections, then model beams using the same section properties in RISA-3D and get full code-checks using AISC 360. This webinar will teach you how to use RISASection quickly and easily to determine complex section properties.
Tapered members are common for metal buildings and pole-type structures. For tapered wide flange members RISA provides a quick way to generate a tapered section that can then be checked per the provisions of AISC Design Guide 25 on tapered wide flanges.
For moment connections in RISAConnection there is an option to place web doubler plates on the column web. These plates act as a reinforcement for the column web to prevent panel zone shear failure. As shown below, when the flanges of a beam in a moment connection connect to a column they form a...
When solving a RISA-3D model you may find you have a Shear UC (unity check) much higher than expected from bending shear alone. If you open the detail report and compare the shear demand to the shear capacity you may see that the demand/capacity is less than the Max Shear Check reported.
When solving a RISA-3D model with hot rolled steel members under the AISC 360-05 (13th Edition) or AISC 360-10 (14th Edition) codes you may find references to a factor called Tau_b. To understand what this factor is you should first be familiar with the Stiffness Adjustment in RISA-3D, then see the...
When solving a RISA-3D model with hot rolled steel members under the AISC 360-05 (13th Edition), AISC 360-10 (14th Edition) or AISC 360-16 (15th Edition) codes you may find that your member deflections are roughly 20% larger than you would expect. To understand why see the AISC 360-10...
Transitioning plates from a circular (or elliptical) to a square (or rectangular) shape can be done easily using some of RISA-3D’s automated generation tools. Below is the procedure for transitioning a circle into a square, but it should be clear how this could be accomplished for other similar...
You can use the full library of international shapes inside of RISAConnection. Currently RISAConnection uses the American steel code AISC code for design checks; however you can customize your connection to use any of the International shapes available in the database.
Our monthly "Structural Moment" newsletter is the best way to keep up with RISA’s product updates, new releases, new features, training events, webinars and more...