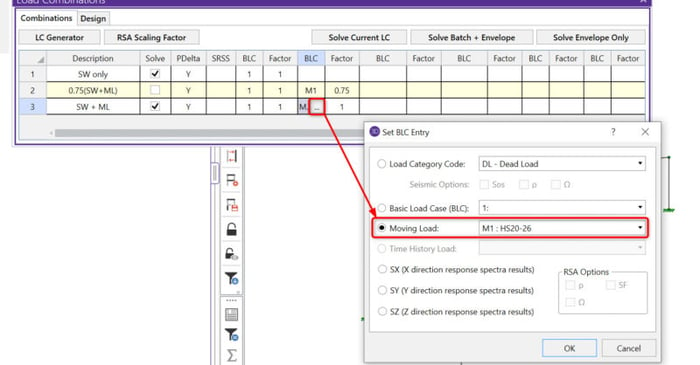
May 27, 2015
Include Moving Load in Batch Solution
With the new release of RISA-3D v13.0, you now have the ability to include moving load combinations in a Batch solution. Just select which load combinations you want included in the Batch solution using the “Solve” checkboxes in the Load Combinations spreadsheet.