Overview
FRP or Fiber Reinforced Polymer (thermoset) composite materials are becoming more and more popular in the construction world of today. There are many reasons for using composite materials, which go beyond the scope of this article but suffice to say that composite/FRP materials are now used in almost every facet of the construction/engineering industries. PulCalc was developed to allow a designer to use RISA-3D data in a model in order to evaluate FRP member capacities.
Pultruded FRP profiles are manufactured worldwide and are very similar to the standard AISC profile geometry found in the “Hot Rolled” Materials section of RISA-3D. The designer can therefore use these standard AISC profiles as they closely match the pultruded profiles of a FRP manufacturer (ex. Creative Pultrusions, Bedford Plastics, etc). When using these members, it’s very important that the user disregard the AISC Code data for FRP members when a model is run due to the fact that the material properties, behavior under load and design constraints are very different than steel! This is where Pulcalc comes in to assist the designer using RISA-3D.
PulCalc Basics
PulCalc V3.0 has several worksheets that look at FRP member capacities as well as connection data. The worksheets available to the user are as follows:
-
Model Properties: Shows typical property values that should be used in RISA-3D
-
Program Properties: Shows Coupon Properties as well as Section Properties. The user can change any of the default values (such as to a specific manufacturer) that work throughout PulCalc.
-
LRFD Members: For LRFD FRP member capacity design. The user can list 50+ members.
-
ASD Members: For ASD FRP member capacity design. The user can list 50+ members.
-
LRFD FRP Connections: This worksheet is for bolted FRP connections. Includes bolt capacities and several FRP connection calculators for LRFD.
-
ASD FRP Connections: This worksheet is for bolted FRP connections. Includes bolt capacities and several FRP connection calculators for ASD.
-
Plate Calculators: There are two (2) calculators, FRP Panel Design and FRP Gusset Plate Design.
It is important that the user selects the worksheet that matches the load combinations and design code established in RISA-3D as well as the new FRP code.
FRP Program Data
PulCalc V3.0 follows the upcoming ASCE/SEI Pultruded FRP LRFD Standard. The material characteristics and factored (or allowable for ASD) data are based on the formulas within the standard and not specific to any manufacturer. As most projects that utilize FRP go through bidding, the Program Properties worksheet lists recommended generic manufacturer coupon properties and is loaded with the same default properties. With V3.0, the user can change the Coupon Property data or the Section Property data to suit a specific manufacturer, resin type or series.
Setting Up a RISA-3D Model
There are a couple different ways that an engineer can set up FRP members in RISA-3D, however the easiest method is to create a New Material through the Data Entry Tables and then set up a New Member under the Hot Rolled Section Sets tab. FRP material properties can be found under the Model Properties worksheet in PulCalc. The model properties listed in red are typically used and can be used in RISA-3D. If a specific manufacturer is going to be used for a project, the user can match the Young’s Modulus (E) and/or Shear Modulus (G) to the material being used within the RISA Material tab. Make sure to also change the Program Properties within PulCalc too.
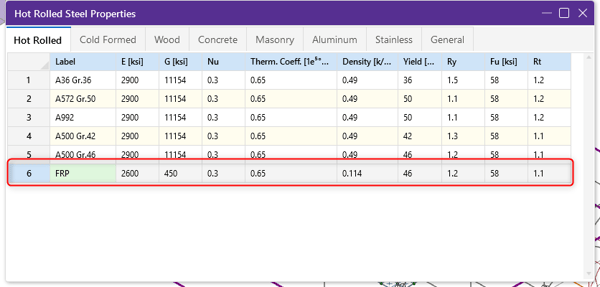
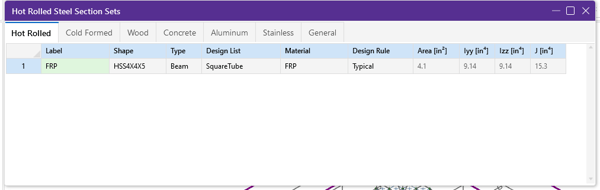
Section Sets are a great way to set up FRP members. Typically, every FRP member should be set up and labeled under Type (such as beams, columns, braces, etc.). Setting up RISA-3D in all other respects is the same as any other created model. These inputs include boundary conditions, joint coordinates, basic load cases and load combinations.
Run the RISA-3D Model
After completing the setup of the model, make sure to run in batch solution (with envelope). The required data can be found by cycling through the individual member detail reports or via RISA’s spreadsheet tables. When evaluating each member, we are interested in the Axial Forces (A) and Bending Stress (Fc) for each FRP member. This data can then be input manually into PulCalc.
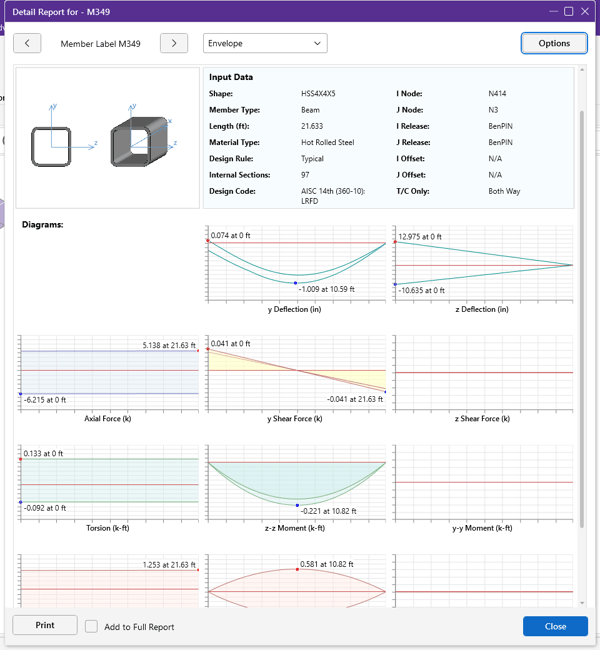
Using PulCalc
With the RISA-3D model results available, open PulCalc. Next, choose the (LRFD or ASD) members worksheet that applies to your analysis and selected design code. An example of an LRFD Members worksheet is shown below.
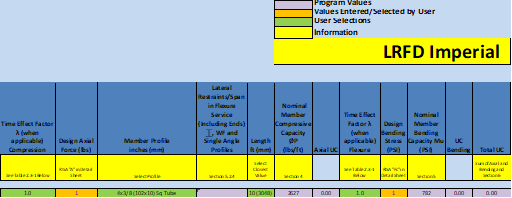
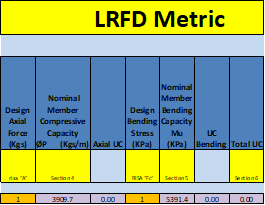
In this LRFD example, we entered both the axial (A) forces and bending (Fc) stresses design data from RISA-3D into the member line (highlighted in orange). The user can then input the selected profile type and member length. With the values from RISA-3D input, the spreadsheet automatically calculates the factored capacities as well as the unity checks for axial, bending and combined forces/stresses. The factored PulCalc capacity figures are based from over 200 internal tables. If any of the unity check values exceeds 1.0, the value is shown in red, indicating there is an issue with the model or member. The ASD functionality is similar.
Note: Engineers can enter up to 50 members on a single member worksheet (LRFD or ASD).
FRP Connections
In the world of FRP structures, connections are perhaps the most important aspect of the design. Determining the proper connections is at times a real challenge. PulCalc evaluates typical connections including bolts, PIN bearing, coped connections, and bolted connections. For bolted connections, the user can select input options such as bolt type, number, size, etc. With the input added, the worksheet will list the capacity check of the bolt(s) as well as the FRP material. These input values are then compared to the shear and tensile strength values.
The new ASCE code disallows FRP clip angles (unless tested). PulCalc V3.0 includes FRP clip angle load tables from one manufacturer. Furthermore, ASCE excludes FRP bolts. PulCalc does provide FRP bolt capacities based on generic manufacturers’ testing.
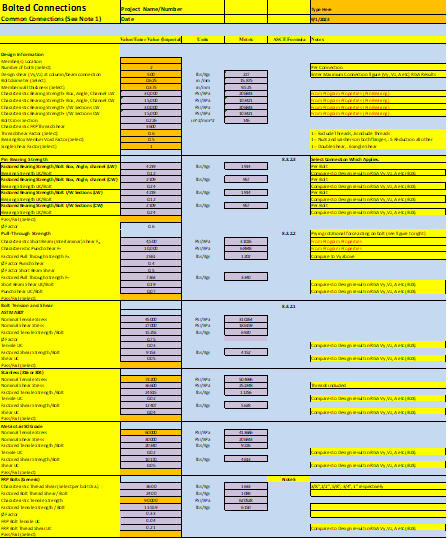
FRP Plate Calculators
Like earlier versions, V3.0 has a FRP Plate Calculator to help the engineer design a supporting frame and panel selection for projects such as telecom. Panel frame spans can be designed based on wind loads and FRP panel type and thickness.
New for V3.0 is a FRP Gusset Plate Calculator for FRP structural connections. Gusset plates are used extensively with FRP connections.
FRP CAD Library
With the significant changes for the new FRP code, we created an optional FRP CAD Library as an option for PulCalc/RISA-3D users. Deliverables are in PDF or dwg formats. The library includes a special telecom deliverable as the telecom sector is especially affected by the new FRP code. Included are typical frames and connection details for common profiles as well as railings and platforms.
FiberDesign offers a couple levels of support including email and even video conferencing. RISA model support is also available as an option where we can help the engineer with model design assistance when working a FRP design model. For more information about PulCalc, click on the link below:
Link: FiberDesign Website